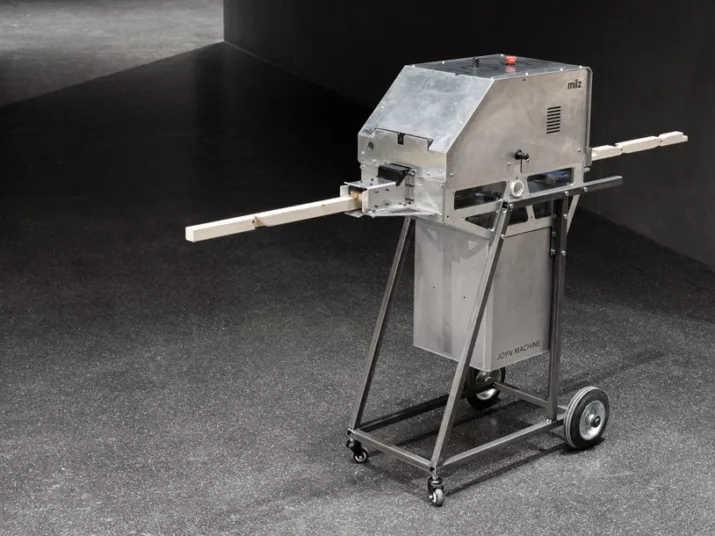
Photo: Studio Milz
Perfect fit
Joyn Machine
Stool, garden bench, 7-metre-high tower: whoever wants to build here doesn’t need to have done an apprenticeship or attained master-craftsman status. Joyn Machine by Berlin-based Studio Milz enables everyone to turn their architectural visions into reality. The principle is very simple: the computer-controlled milling machine transforms ordinary wooden slats from the DIY store into a 3D construction kit. In a few easy steps, the finished parts can then be assembled into chairs, benches or even entire houses.
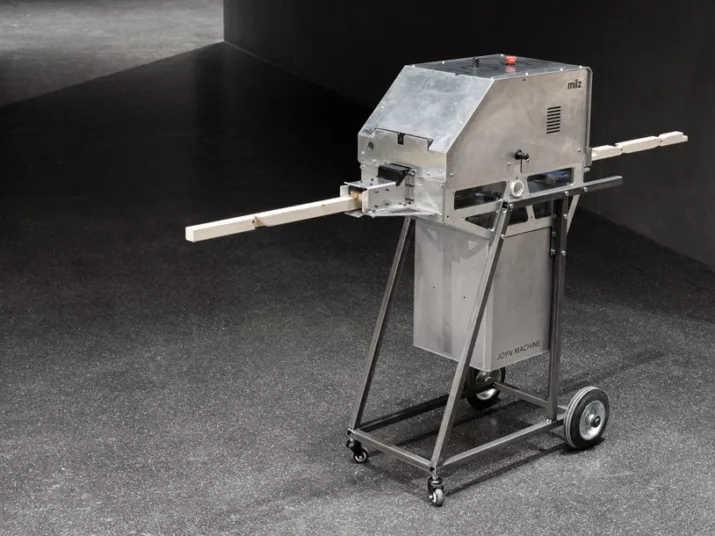
Photo: Studio Milz
The right framework conditions
Simon Deeg and Andreas Picker have already built many interesting machines. Their drawing robots, wind-powered clocks or experimental seeders aim to animate people to deal creatively with technology. They’re particularly keen on combining digital and analogue elements. In the case of the Joyn Machine, the end result is assembled by hand, combining both worlds: physical and digital, slats and data, high-tech and low-tech.
Deeg explains: “Actually, we came up with the original idea at university. At the time, we’d been working a lot with wooden boards from the DIY store. And because as designers we were also dealing with digital tools, we wanted to combine the two. With a machine that takes over certain manual tasks, but at the same time provides a clear framework for carrying out the other tasks. It enables us to build simple frame structures such as a pavilion, but also pieces of furniture such as stools and benches. Everything, really – from small everyday products to commercial utility buildings and even bridges.”
Neither screws nor nails
The Joyn Machine takes care of the entire manufacturing chain, from designing to producing individual wooden parts. The digital aspect of the Joyn Machine is its software, which can be used to design different objects. It calculates a 3D model that can be manufactured with the mobile milling machine.
A small screen then guides users step by step through the simple process: insert slat, mill, turn and remove component. The good thing: the software calculates all the joints in such a way that nails and glue are largely superfluous and the construction is absolutely safe. The resulting kit now only needs to be assembled by hand. Another advantage is that, at a weight of around 100kg, the CNC machine is so light it can quickly be rolled to wherever it is required.
Carpenter today, architect tomorrow
Futurium exhibits several examples produced by Studio Milz in collaboration with architect Patrick Bedarf and industrial designer Dustin Jessen. These pieces of furniture can also be built by visitors themselves in workshops. Patrick Bedarf explains that “any Tom, Dick or Harry can get creative here themselves”. Dustin Jessen adds: “The Joyn Machine works like a 3D printer. You don’t have to be a trained carpenter to create relatively complicated joints and constructions.”
Those who want to get involved here don’t need any previous knowledge of woodwork, design, architecture or structural engineering. In other words: anyone who can work a simple smartphone app can also operate the Joyn Machine. Via live video on the connected tablet, users can even see what’s currently happening inside the machine.
Easy-peasy construction
This collaborative approach is crucial to Studio Milz: everyone can be creative and get right down to work. Either with their own designs or with practical suggestions from an online catalogue. The team built an entire pavilion that’s exhibited in the Lab as a great walk-through example. “We integrated table and seating areas in the lower segment, but also wanted to emphasise the architectural aspect: with the Joyn Machine, we’re able to build high constructions, create a roof, a shelter or a retreat,” Bedarf says. “In short, we wanted to show what a wide spectrum you can cover, even with limited resources.”
Due to their airy design, the structures and pieces of furniture are not only easy to build, but also really light in weight. Feel like having a go? We recommend you head to one of the workshops right here at Futurium.
Advantage: wood
Although further features are envisioned for the Joyn Machine, the material used will remain the same for the time being. Simon Deeg reveals he’s a big fan of wood as building material. “It’s just tremendous fun to work with.” Dustin Jessen adds: “Wood offers great advantages. You can use many different types of wood. And the plug-in connections allow for huge variety and variability. From this perspective, the machine opens up virtually limitless possibilities. Particularly in view of the scarcity of resources and the problems arising from construction methods using reinforced concrete, wood is a good, sustainable alternative in architecture too.”
And, finally, there’s currently a revival of wood construction, which is due in part to modern manufacturing methods such as the Joyn Machine. They enable so-called mass customisation, whereby each part is made individually as required. “Out of the 250 pieces used to build this pavilion, for instance, only a very few – around 10 per cent – are similar or identical. So nearly every slat and component is completely different,” explains Simon Deeg. “And by means of the digital model, you could now easily rebuild this pavilion in Tokyo, London or Los Angeles – or slightly modify it and then bring the knowledge back into the software.”
Think big, produce small
One aspect is particularly important to the creators, namely the creative collaboration between human and machine. And it doesn’t always run smoothly and predictably – a fact that the Joyn Machine does not shy away from reflecting in the design process. “Digital fabrication often creates perfect visions of perfect worlds, but we all know that life isn’t perfect, linear or predictable,” says Patrick Bedarf. And his colleague Dustin Jessen emphasises: “During the design process, you always need to remember that you’re designing for other people. The technology behind it, and what it’s able to do, shouldn’t be the focus.”
Instead, Studio Milz is all about opening up and democratising design and architecture, because “the future is always an act of creation. If we’re a part of this act, we can actively shape that future.”